We decided to finally make an attempt to build a Dingbot robot based on the girl genius web comics.
Please note, this material is provided for informational purposes only and is not a guide on how to create the designs. Please take a look at our disclaimer.
Our design is based on the first BingBot, a small robot similar to a pocket watch. Below is a image of a GirlGeniusOnline Dingbat in action.
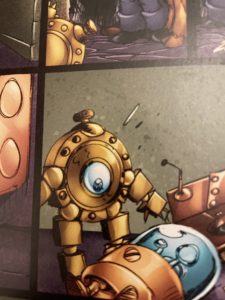
As the series continue she create a variety of different BingBots and even Wingbots.
After we have settled on a design on paper we like laying out all the components on our workbench and start visualizing how the pieces fit together and to make sure we have all the parts we need.
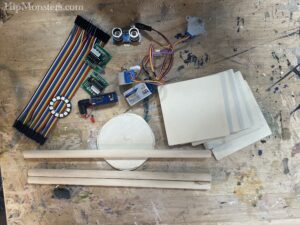
We made the design as small as possible but still fit all the electronics including a RaspberryPi Nano. We wanted the design to be a fully functioning computer. The idea was when it is not running about it can be used to play music or video games.
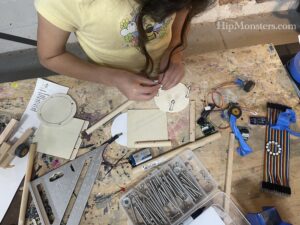
The front and back to the robot are plywood circles that will serve as bases for all the electronics. To make sure the two sides align, we clamped two pieces of plywood together and used coping saw. To smooth out any irregularities, clamped them together again and sanded them repeatedly.
We used 2 inch bolts to separate the front and back plates. The is the smallest width that will still be able to hold all of our electronics. After repeated measuring, we drilled the holes while they were still clamped. This assured the bolts would align. Since the bolts are part of the atheistic of the robots it is important to get the positions correct.
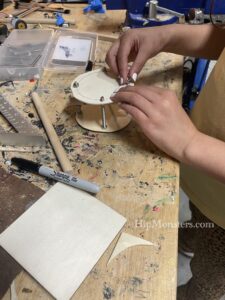
We used three nuts and four washers per bolts to acts as spacers. To keep the bolts from loosing we used lock bolts (which can prove difficult to put on) and a pneumatic tubing in between the top and bottom bolts. We have used pneumatic tubing as spacers before in our robot designs and it works great even after years of use.
Once the two plates were secured we cut a strip of plastic to seal the gap. We thought using the side to access the components would be a unique and useful design. Normally, we prefer to have most of the electronics exposed but dingbot has a clean and elegant design. We recommend testing your layout of a sheet of paper first before cutting the holes in the plastic.
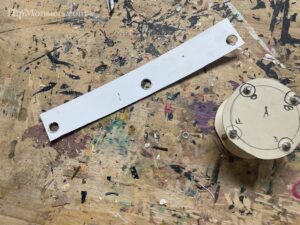
After a few trial and error we managed to secure the plastic strip. The first one broke so the second time we heated it with a blow dry to make it more flexible.
Down the center of the robots is a wooden dowel which will server as the spine for the robots. The legs and arms will both be anchor to the spine.
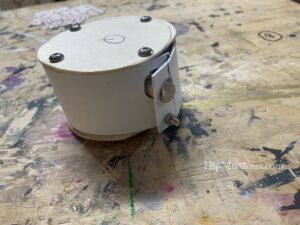
Here is a bottom view showing the spine.
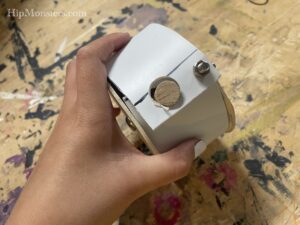
We are not 100 percent happy with how the plastic strip pops out but we will try applying low heat again and try and mold it into shape.
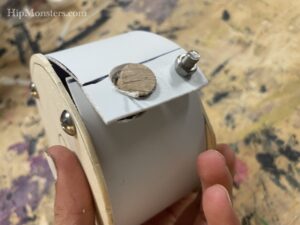
Although you cannot see them, the design fits a RaspberryPi Nano, two motors, h-bridges, tons of wiring and a battery neatly.
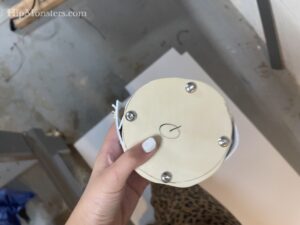
Next step is to design the legs! We are leaning towards a toy robot inspired design.
Happy creating!